Projekt 24
Motivation and objectives
Cast Part Feasibility Assessment Method
Motivation and objectives
In-service performance of cast parts not only depends on part design, but also on manufacturing effects like part orientation in mold, gating & feeder system (size, location) and process parameters (filling rates, melt & die temperatures). Casting process restrictions and requirements are of equal importance as attribute requirements (strength, durability, NVH, crash).
Conventional component optimization relies on expert skills and expert guided analysis loops. MDO tools as well as design engineers require fully automated tools & expert systems to evaluate the feasibility and quality of cast parts upfront, quantitatively and efficiently.
The objective is to develop an automatic tool set to run casting simulations, to quantify existing casting process know-how, to make it available for automatic evaluation schemes and to provide validation example parts.

Approach
Approach
- Expert system "Input Specification" - develop an automatic tool to specify initial casting process conditions (orientation, gating & feeder system, process temperatures, filling parameters) based on best-practice rules for a given casting design. This is a prerequisite for MDO with casting simulation included.
- Casting simulation - automatic meshing (as-cast geometries), automatic multiple batch mode analyses, automatic data import/ export, result mapping.
- Expert system "Feasibility & Quality" - develop an assessment tool based on casting simulation results to evaluate design proposals of chassis castings (may be extended to body castings) with respect to casting feasibility (completely filled) and cast part quality (e.g. defect distribution and cast part properties with an impact on mechanical properties, attribute requirements and component performance).
- Calibration and validation - develop demonstrator components to calibrate the "Feasibility & Quality" assessment tool. Design related test conditions, tailored to feature and test the most relevant phenomena in cast parts like incomplete filling, porosity, inhomogeneous microstructure or misrun problems. Run casting trials with modular casting tools with a variety of demonstrator design proposals and process conditions. Validate the final feasibility assessment system using real cast parts.
Partners
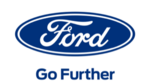
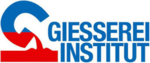